Предел прочности стали при повышенных температурах
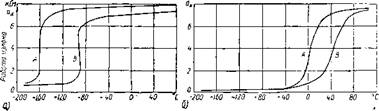
ВНУТРЕННИЕ УСИЛИЯ И ДЕФОРМАЦИИ ПРИ СВАРКЕ
Механические свойства металла изменяются в зависимости от его температурного состояния. В процессе сварки металл подвергается нагреву до высоких температур, изменение которых происходит в широких пределах и в сравнительно короткое время.
Механические характеристики металла при высоких температурах нельзя считать полностью исследованными. Более обстоятельно изучены механические свойства металла в области упругих изменений. На фиг. 9 представлено изменение механических характеристик стали в зависимости от температуры при нагреве до 500—600° С [2].
Модуль упругости стали Е при нагревании постепенно понижается, а коэффициент теплового расширения а возрастает. В области температур упругих изменений стали произведение аЕ можем принять постоянным и равным (хЕ = 12 • 10-6 • 2,1 • 106^ = 25 кГ/см2.
Предел прочности стали оь с повышением температуры до 100°С несколько снижается, затем при дальнейшем нагреве повышается и имеет наибольшее значение в области температур 200—300°С. При нагреве от 300 до 500°С предел прочности стали, кроме жароупорной, постепенно понижается. При температуре выше 500°С предел прочности стали резко снижается, принимая при 600°С весьма низкие значения по сравнению с прочностью при обычных температурах.
Пластические свойства стали, характеризуемые относительным удлинением и поперечным сужением при разрыве, неск(элько снижаются в области температур 150—300° С. С увеличением температуры выше 300°С пластические свойства стали возрастают. Такой характер изменения пластических свойств стали показывает, что при большой скорости остывания закрепленного стального элемента его разрыв при температурах 150—300°С весьма вероятен. Этим объясняется целесообразность предварительного подо-
21
грева стали при сварке до 150—200° С, чтобы замедлить остывание после сварки.
Предел текучести стали ст с повышением температуры до 500° С несколько понижается, а затем при дальнейшем повышении температуры (свыше 500°С) резко падает, доходя почти до нуля при температуре 600°С.
Фиг. 9. Зависимость механических свойств стали от температуры.
В действительности предел текучести стали несколько повышается в области температур 150—300°С, затем постепенно понижается при нагреве до 500° С, а после этого резко падает (фиг. 10, пунктирная кривая). Ввиду малых значений предела текучести стали при температуре 600°С и выше, примем допущение, что предел текучести сталей, кроме жароупорной, при температуре 600° С и выше имеет нулевое значение (фиг. 11). Другими словами, будем считать, что при температуре 600°С и выше сталь находится только в пластическом состоянии, теряя полностью свои упругие свойства.
При охлаждении стали ниже нуля предел прочности и предел текучести повышаются, причем предел текучести приближается к пределу прочности.
При весьма низкой температуре сталь теряет пластические свойства, переходит в хрупкое состояние и становится хладно-
Фиг. 10. Зависимость предела текучести аг стали
от температуры:
1 — схематизированная диаграмма; 2 — действительная диаграмма.
бгшКГ/СМ>
Фиг. 11. Условная зависимость предела текучести стали от температуры:
1 — схематизированная диаграмма; 2 — условная диаграмма.
ломкой. Для каждого металла существует своя критическая температура, выше которой металл способен пластически деформироваться, а при температурах ниже критических металл теряет способность к образованию пластических деформаций и разрушается в виде хрупкого излома. Для стали критическая температура, ниже которой происходит хрупкое разрушение, находится в области — 65—160° С.
Помимо низких температур, на хрупкое разрушение стали большое влияние оказывает концентрация напряжений, вызванная
Фиг. 12. Работа излома стали при разных температурах; а — ненадрезанные образцы; б — надрезанные образцы.
надрезами и неровностями. Хрупкое состояние стали может быть вызвано объемным напряженным состоянием, при котором весьма затруднено образование пластических деформаций.
На фиг. 12 приведены кривые ударной вязкости котельной стали в зависимости от температуры [3]. Кривые А соответствуют результатам испытаний стали, подвергавшейся предварительно нормализации для измельчения зерна, а кривые В соответствуют результатам испытаний крупно-зернистой стали.
Критическая температура ненадрезанных образцов для стали А— 160°С, а для стали В—90°С. При наличии надрезов критическая температура хрупкого разрушения значительно выше и для стали А равна +5° С, а для стали В +45° С (см. фиг. 12).
Для устранения деформаций после ‘сварки – применяется холодная и горячая правка сварных конструкций. Холодная правка основана на растяжении укороченных участков и мест сварной конструкции до проектных размеров – и форм. …
Образование остаточных напряжений и деформаций при сварке вызывается появлением внутренних усилий при местном нагреве металла. Оба эти явления находятся во взаимной связи, но проявляются при сварке конструкций в различной степени …
могут быть самые разнообразные и зависят от характера соединений и вида конструкции, применяемых методов сварки, режима нагрева, механических характеристик и химического состава свариваемых металлов. Как правило, для уменьшения пиков остаточных …
Источник
Марка стали | Т, º С | Rp0.2, МПа | Rm, МПа | Е, ГПа | α, мкК-1 |
Ст3сп5 Лист, S | 20 | 245.0 | 373.0 | 200 | 11.5 |
Марка стали | Т, º С | [σ], МПа | 1,3[σ], МПа | [σ]RV, МПа |
Ст3сп5 Лист, S | 20 | 143.5 | 186.6 | 373.0 |
Марка стали | Т, º С | Rp0.2, МПа | Rm, МПа |
Ст3сп5 В горячекатанном состоянии | 20 | 245 | 370 |
Марка стали | Т, º С | Rp0.2, МПа | Rm, МПа |
Ст3сп5 Горячкатаный и холоднокатаный лист в термически обработанном состоянии | 20 | – | 370 |
Марка стали | Т, º С | Rp0.2, МПа | Rm, МПа |
Ст3сп5 – | 20 | 245 | 370 |
Марка стали | Т, º С | Rp0.2, МПа | Rm, МПа |
Ст3сп5 – | 20 | 260 | 412 |
Назначение:
Листы по ГОСТ 14637-89 категории 2, 3 и 6 – несущие элементы сварных и несварных конструкций и деталей, работающих при положительных температурах. Листы категории 5 – несущие элементы сварных конструкций, работающих при переменных нагрузках: толщиной до 25 мм – в интервале температур от -40 до +425 град.: при толщине свыше 25 мм – в интервале температур от -20 до + 425 град.; при условии поставки с гарантируемой свариваемостью.
Листы для электросварных труб, работающих при температуре до 300 град. и давлении до 1,6 МПа. Детали котлов и трубопроводов, выполненные из листа толщиной до 12 мм, и кованые детали, предназначенные для эксплуатации при температуре до 200 град. и давлении 1,6 МПа.
Rp0.2 – минимальное значение предела текучести при расчетной температуре, МПа (Н/мм2).
Определение: под пределом текучести понимается то напряжение,
при котором происходит рост деформации без заметного увеличения нагрузки. В тех случаях
, когда на диаграмме отсутствует явно выраженная площадка текучести
, за предел текучести условно принимается величина напряжения
, при котором остаточная деформация составляет 0,2%.
Rm – минимальное значение предела прочности (временного сопротивления) при расчетной температуре, МПа (Н/мм2)
.
Определение: отношение максимальной силы, которую способен выдержать образец
, к его начальной площади поперечного сечения носит название предела прочности или временного сопротивления
. Предел прочности также является условной величиной.
Е – модуль упругости при расчетной температуре, МПа (Н/мм2)
.
Определение: модуль упругости представляет собой коэффициент пропорциональности
, устанавливающий связь между напряжением и деформацией σ = Eε
. Модуль упругости является физической константой материала и определяется экспериментально
. Единица измерения модуля упругости в вышеприведенных таблицах – ГПа (1ГПа = 1000 МПа).
α – коэффициент линейного расширения при расчетной температуре (коэффициент температурного расширения материала)
.
Определение: коэффициент температурного расширения
– характеризует относительную величину изменения линейных размеров тела с изменением температуры
α = ΔL/LΔT.
[σ] – номинальное допускаемое напряжение.
Определение: допускаемое напряжение
– это отношение некоторого предельного напряжения для данного материала к коэффициенту запаса.
Номинальное допускаемое напряжение определяют по характеристикам материала
при расчетной температуре.
В качестве некоторого предельного напряжения (т.е. характеристики материала) принимают – предел текучести
, предел прочности, предел длительной прочности.
1.3[σ] – расчетная группа категорий напряжений (σ)2 (ПНАЭ Г-7-002-86)
. В общем случае, это допускаемое напряжение для оценки приведенных напряжений, определяемых по суммам составляющих общих
или местных мембранных и общих изгибных напряжений (σ)2 = [σm или σmL] + σb
.
[σ]RV – расчетная группа категорий напряжений (σ)RV (ПНАЭ Г-7-002-86)
. Это допускаемое напряжение для оценки размаха напряжений, определяемого по суммам составляющих общих
или местных мембранных, общих или местных изгибных, общих температурных и компенсационных напряжений
(σ)RV = [σm или σmL] + σb
+ σbL + σT + [σkm или σkmL] + σkb + τks
.
ВАЖНО!
1 При повышенных температурах значение допускаемого напряжения определяется без учета длительных характеристик прочности (т.е. предела длительной прочности).
2 Физико-механические характеристики материалов приняты согласно ПНАЭ Г-7-002-86. Промежуточные значения характеристик материала определяются линейной интерполяцией.
3 Справочные данные, приведенные на сайте, имеют статус “ознакомительный” и не могут заменить использование официальных источников (ПНАЭ, ГОСТы и т.п.).
Источник
Содержание:
- Влияние высоких температур на механические свойства металлов.
Влияние высоких температур на механические свойства металлов.
- Влияние высоких температур на механические свойства металлов. С бурным развитием машиностроения все большее значение приобретает расчет прочности механических деталей, которые длительное время работают при высоких температурах. К таким частям относятся, например, диски и лопатки паровых и газовых
турбин, трубы и другие детали паровых котлов, различные детали двигателей внутреннего сгорания, реактивных двигателей и др. Поведение материала под нагрузкой такой детали влияет как на абсолютное значение температуры, так и на время работы
детали, особенно при этой температуре. Однако метод обычных
Людмила Фирмаль
кратковременных испытаний основан на том, что при относительно низких температурах (например, до 300-400°, до 350°, до 50-150 ° для цветных металлов) прочностные и пластические характеристики металлов выше, чем у цветных металлов, в то время как знание свойств металлов при обычных (комнатных) температурах существенно зависит от продолжительности самого испытания.
В результате определение свойств металла, например, пропорционального предела текучести или предела текучести, при температуре не менее 400 ° С для стали и более 150 ° С для цветных металлов является условным. По мере повышения температуры модуль упругости и предел пропорциональности металла вначале постепенно уменьшается, а затем уменьшается все более резко,
- начиная с указанной выше температуры. Так, величина нормального модуля упругости стали при температуре 600°составляет около 25-30%, а при температуре 800°она примерно на 50% ниже его значения при комнатной температуре. Предел уменьшения и пропорциональности модуля упругости в цветных металлах еще более выражен. Величина коэффициента поперечной деформации стали с повышением температуры обычно незначительно возрастает. Предел текучести углеродистой стали с повышением температуры
обычно вначале незначительно возрастает и достигает своего максимума при температуре около 200°. При дальнейшем повышении температуры предел текучести значительно снижается, поэтому при температуре 400° предел текучести углеродистой стали составляет всего 60-70% при комнатной температуре. При этом длина предела текучести уменьшается, и примерно при 350-450°с углеродистой стали этот участок полностью исчезает. В легированной стали предел текучести снижается с повышением температуры
. Величина отношения предела текучести к пределу прочности стали при повышении температуры, как правило, дополнительно увеличивает температуру, а при температуре 300-350° величина этого отношения
Людмила Фирмаль
составляет 0,35-0,4. Пластические свойства стали (общее удлинение и усадка при разрыве) с повышением температуры от 20 до 200 до 300 е несколько снижаются; с дальнейшим повышением температуры пластичность стали снижается, как правило. Сталь, хром-вольфрамовая сталь). В аустенитных хромоникелевых сталях пластичность снижается с повышением температуры, в углеродистых сталях при температурах 250-350°(так называемая синеломкость стали) и в некоторых цветных металлах (алюминий, магний) при температуре 900-1000°(покраснение стали) повышение температуры вызывает непрерывное повышение, а в других (медь, латунь, никель, наоборот). удлинение и усадка Предел прочности стали при повышении температуры, как правило, повышается первым, а при
температуре 250-300°достигает максимального значения, которое примерно на 20-25% превышает значение предела прочности при комнатной температуре. При дальнейшем повышении температуры величина предела прочности на растяжение резко снижается. Например, для низкоуглеродистой стали 600°прочность на растяжение составляет всего около 40% от прочности на растяжение той же стали при комнатной температуре. Добавление легирующих примесей (никеля, хрома, ванадия) задерживает снижение прочности стали на растяжение при повышении
температуры. Прочность на растяжение чугуна до 300°остается практически неизменной; при дальнейшем повышении температуры она значительно снижается. В цветных металлах(алюминий, медь, латунь, магний, олово, свинец, цинк, никель) и их сплавах прочность на растяжение уменьшается непрерывно и сильно с повышением температуры, поэтому при 600°этих металлов величина прочности на растяжение составляет лишь несколько процентов от величины прочности на растяжение до комнатной температуры. Изменение
предела выносливости стали с повышением температуры приводит к изменению предела прочности, то есть сначала предел выносливости незначительно увеличивается, а затем непрерывно снижается. Фигура. 658*. В качестве примера приведем рисунок. На рис. 658 показаны кривые изменения прочностных и пластических свойств низкоуглеродистой стали (0,15°С) при повышении температуры до 800°С.
Смотрите также:
- Примеры решения задач по сопротивлению материалов: сопромату
Источник
Прочность металлических конструкций – один из важнейших параметров, определяющих их надежность и безопасность. Издревле вопросы прочности решались опытным путем — если какое-либо изделие ломалось — то следующее делали толще и массивнее. С 17 века ученые начали планомерное исследование проблемы, прочностные параметры материалов и конструкций из них можно рассчитать заранее, на этапе проектирования. Металлурги разработали добавки, влияющие на прочность стальных сплавов.
Предел прочности стали
Предел прочности
Предел прочности — это максимальное значение напряжений, испытываемых материалом до того, как он начнет разрушаться. Его физический смысл определяет усилие растяжения, которое нужно приложить к стрежневидному образцу определенного сечения, чтобы разорвать его.
Каким образом производится испытание на прочность
Прочностные испытания на сопротивление разрыву проводятся на специальных испытательных стендах. В них неподвижно закрепляется один конец испытываемого образца, а к другому присоединяют крепление привода, электромеханического или гидравлического. Этот привод создает плавно увеличивающее усилие, действующее на разрыв образца, или же на его изгиб или скручивание.
Испытание на разрыв
Электронная система контроля фиксирует усилие растяжения и относительное удлинение, и другие виды деформации образца.
Виды пределов прочности
Предел прочности — один из главных механических параметров стали, равно как и любого другого конструкционного материала.
Эта величина используется при прочностных расчетах деталей и конструкций, судя по ней, решают, применим ли данный материал в конкретной сфере или нужно подбирать более прочный.
Различают следующие виды предела прочности при:
- сжатии — определяет способность материала сопротивляться давлению внешней силы;
- изгибе — влияет на гибкость деталей;
- кручении – показывает, насколько материал пригоден для нагруженных приводных валов, передающих крутящий момент;
- растяжении.
Виды испытаний прочности материалов
Научное название параметра, используемое в стандартах и других официальных документах — временное сопротивление разрыву.
Предел прочности стали
На сегодняшний день сталь все еще является наиболее применяемым конструкционным материалом, понемногу уступая свои позиции различным пластмассам и композитным материалам. От корректного расчета пределов прочности металла зависит его долговечность, надежность и безопасность в эксплуатации.
Предел прочности стали зависит от ее марки и изменяется в пределах от 300 Мпа у обычной низкоуглеродистой конструкционной стали до 900 Мпа у специальных высоколегированных марок.
На значение параметра влияют:
- химический состав сплава;
- термические процедуры, способствующие упрочнению материалов: закалка, отпуск, отжиг и т.д.
Некоторые примеси снижают прочность, и от них стараются избавляться на этапе отливки и проката, другие, наоборот, повышают. Их специально добавляют в состав сплава.
Условный предел текучести
Кроме предела прочности, в инженерных расчетах широко применяется связанное с ним понятие-предел текучести, обозначаемый σт. Он равен величине напряжения сопротивления разрыву, которое необходимо создать в материале, для того, чтобы деформация продолжала расти без наращивания нагрузки. Это состояние материала непосредственно предшествует его разрушению.
На микроуровне при таких напряжениях начинают рваться межатомные связи в кристаллической решетке, а на оставшиеся связи увеличивается удельная нагрузка.
Общие сведения и характеристики сталей
С точки зрения конструктора, наибольшую важность для сплавов, работающих в обычных условиях, имеют физико-механические параметры стали. В отдельных случаях, когда изделию предстоит работать в условиях экстремально высоких или низких температур, высокого давления, повышенной влажности, под воздействием агрессивных сред — не меньшую важность приобретают и химические свойства стали. Как физико-механические, так и химические свойства сплавов во многом определяются их химическим составом.
Влияние содержание углерода на свойства сталей
По мере увеличения процентной доли углерода происходит снижение пластичности вещества с одновременным ростом прочности и твердости. Этот эффект наблюдается до приблизительно 1% доли, далее начинается снижение прочностных характеристик.
Повышение доли углерода также повышает порог хладоемкости, это используется при создании морозоустойчивых и криогенных марок.
Влияние углерода на механические свойства стали
Рост содержания С приводит к ухудшению литейных свойств, отрицательно влияет на способность материала к механической обработке.
Добавки марганца и кремния
Mn содержится в большинстве марок стали. Его применяют для вытеснения из расплава кислорода и серы. Рост содержания Mn до определенного предела (2%) улучшает такие параметры обрабатываемости, как ковкость и свариваемость. После этого предела дальнейшее увеличение содержания ведет к образованию трещин при термообработке.
Влияние кремния на свойства сталей
Si применяется в роли раскислителя, используемого при выплавке стальных сплавов и определяет тип стали. В спокойных высокоуглеродистых марках должно содержаться не более 0,6% кремния. Для полуспокойных марок этот предел еще ниже — 0,1 %.
При производстве ферритов кремний увеличивает их прочностные параметры, не понижая пластичности. Этот эффект сохраняется до порогового содержания в 0,4%.
Влияние легирующих добавок на свойства стали
В сочетании с Mn или Mo кремний способствует росту закаливаемости, а вместе с Сг и Ni повышает коррозионную устойчивость сплавов.
Азот и кислород в сплаве
Эти самые распространенные в земной атмосфере газы вредно влияют на прочностные свойства. Образуемые ими соединения в виде включений в кристаллическую структуру существенно снижают прочностные параметры и пластичность.
Легирующие добавки в составе сплавов
Это вещества, намеренно добавляемые в расплав для улучшения свойств сплава и доведения его параметров до требуемых. Одни из них добавляются в больших количествах (более процента), другие — в очень малых. Наиболее часто применяю следующие легирующие добавки:
- Хром. Применяется для повышения прокаливаемости и твердости. Доля – 0,8-0,2%.
- Бор. Улучшает хладноломкость и радиационную стойкость. Доля – 0,003%.
- Титан. Добавляется для улучшения структуры Cr-Mn сплавов. Доля – 0,1%.
- Молибден. Повышает прочностные характеристики и коррозионную стойкость, снижает хрупкость. Доля – 0,15-0,45%.
- Ванадий. Улучшает прочностные параметры и упругость. Доля – 0,1-0,3%.
- Никель. Способствует росту прочностных характеристик и прокаливаемости, однако при этом ведет к увеличению хрупкости. Этот эффект компенсируют одновременным добавлением молибдена.
Металлурги используют и более сложные комбинации легирующих добавок, добиваясь получения уникальных сочетаний физико-механических свойств стали. Стоимость таких марок в несколько раз (а то и десятков раз) превышает стоимость обычных низкоуглеродистых сталей. Применяются они для особо ответственных конструкций и узлов.
Источник